Addressing Fire and Explosion Risks in EVs and ESSs
The continuous increase in energy demand, as well as improved performance are simulating the rapid maturing of lithium-ion batteries in large energy applications such as electric vehicles (EV) and various renewable energy storage systems (ESS). However, the rapid increase in battery usage, energy density, and high-speed charging and discharging comes with a rise in fire and explosion incidents. Recent combustions of 3C products have instigated a widespread fear of using lithium batteries and news coverage of EVs that caught fire during or after charging has even raised people’s doubts about buying EVs. Recurrent ESS combustions in South Korea has caused the rapid expansion of ESSs around the globe to slow down.
Causes of Lithium-ion Fires: Metal Burrs and Particles
Most fire accidents of Li-ion batteries are initiated by severe inflammation and it is difficult to analyse the actual cause. Common reports contain the electrical control system errors or the lithium metal deposition compiling over a long time and growing into lithium dendrite, which cause internal short circuits in the battery. Although these are certainly possible factors, detailed analysis shows that they are difficult to establish in the bulk of battery accidents due to acute cluster chemical combustion. Test reports and battery cell manufacturers avoid the topic of how spontaneous internal short circuits are induced in Li-ion batteries, if not by lithium dendrite. Metal burrs or particles that puncture or exist in the separator may be a possible cause. The reason why existing manufacturing processes fail to identify this remains unclear. Although the defective rate is not high and the amount is considered acceptable, accidents that occur on the market, in the storage plant, or finished vehicle, or even impact the lives of people are highly newsworthy.
Dangers in Charging Li-ion Batteries
In addition, most fire accidents in Li-ion batteries occur while charging. The main reason is that the negative electrode materials used in Li-ion batteries could inflate, causing potential defective products that have not been short-circuited to become internal short circuits. Research has shown that this inflation will continue to expand repeated charge and discharge cycles, so that the danger will even extend to the user when using the battery. This means that although the battery may not have internally short-circuited during production when the separator is partially pierced by metal burrs or particles, there is a risk that such defects from a common production process cannot be effectively detected. The most prevalent problems in production inspection on battery cells are ① too low dry cell (jelly roll) insulation test voltage (<350V), and ② flashover that temporarily damages the separator and cannot be detected by general insulation testers.
Chroma ATE recommends including these two as standard test items during battery cell inspection:
– Jelly roll insulation test voltage must be over (350V + α) peak value (Figure 1).
– Voltage/current flashover shall not occur during the insulation/withstand voltage test (Figure 2).( Concept referred to general electrical safety regulation.)
Chroma’s experts have drawn these conclusions from examining large numbers of analysis reports, research documents, and long-term experiments. Correct jelly roll insulation testing is a highly effective and low-cost method to prevent Li-ion batteries from catching fire.
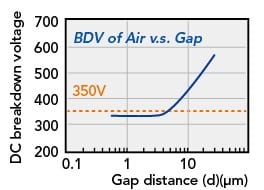
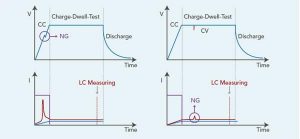
Major international car battery manufacturers have recently adopted Chroma’s two unique technologies as well as the above two recommendations to ensure the safety and quality of their battery cells.
With well over 30 years of experience in testing and technology for power electronics, Chroma ATE continues to ride the wave. The test equipment manufacturer drives testing solutions for EV-related industries to ensure the safety, quality, and reliability of your products.
Chroma 11210 Battery Cell Insulation Tester is specifically designed for the detection of abnormal insulation of lithium-ion batteries (dry cells). The tester offers two unique technologies that other withstand voltage or insulation testers on the market do not have. Chroma 11210 not only monitors the entire process of testing for flashover due to abnormal partial discharge in the battery cell but also quantifies it in numbers and recordable waveforms. Moreover, after reaching the test voltage, the leakage current or insulation resistance will be measured and judged as abnormal during the test time like using WV/IR testers.
View all Chroma products available from MDL Technologies
Want further information, advice or a quote? Speak with our expert consultants about any of the Chroma products available on 01462 431981, or contact us here.