EV Component Testing
OBC/DC-DC Converter ATS∣8000
On-Board Chargers (OBC) convert grid power into DC current to charge the on-board energy storage device. In addition to all the functions of the general OBC, the Bi-directional OBC (BOBC) can also output the stored power for applications such as V2L, V2V, and V2G. The DC/DC converter converts the high voltage DC power to low voltage for the auxiliary power output of the EV battery.
Chroma has a complete line of AC and DC power load products. We provide automatic test systems for OBCs and DC/DC converters that verify the performance and safety of your products according to their characteristics and test requirements. The systems are especially suitable for R&D verification, QA and production lines of EV parts manufacturers
and EV factories.
Key Features
- Built-in standard test items compliant with QC/T 895, GB/T 24347, GB/T 40432, SAE J2894 standard requirements that can be loaded directly without reprogramming
- Panel controllers with standard wiring solve wiring difficulties, improve reliability and shorten test time
- Supports periodic/uninterrupted CAN Bus transmission
- DBC file loading allows convenient retrieval of CAN signal parameters
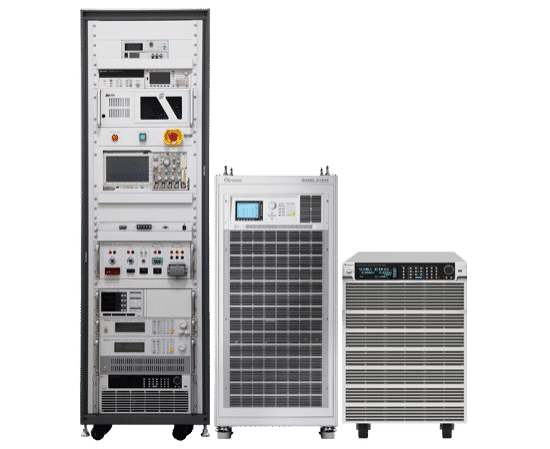
PEU ATS∣8000
The PEU (Power Electronics Unit) is an all-in-one electric vehicle component that integrates OBCs, DC/DC Converters, PDUs (Power Distribution Units), and others. There are various ways to integrate these components according to different needs. By reducing costs and simplifying the interior design of the EV, it sets a trend for future suppliers. Among these components, the PDU is responsible for distributing battery power to other components through each respective channel. Although its task is straightforward, it must withstand high currents, which can easily cause severe damage to the vehicle due to poor design or faulty assembly. The ATS can be used to simulate various related scenarios, such as high/ low voltage limit, withstand current, signal switching, and CAN communication, providing a
rigorous testing regime.
Key Features
- Customized and automatic switching fixture for increased test efficiency
- Supports periodic/uninterrupted CAN Bus transmission
- DBC file loading allows convenient retrieval of CAN signal parameters
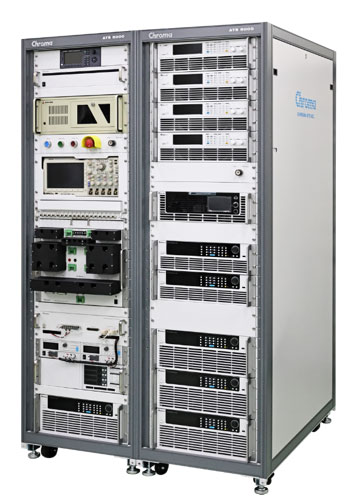
LV124 ATS RTStand LV124 Pro F24
The vehicle’s windshield wipers, audio-visual system, steering assistance, and even its self-driving system all rely on auxiliary power supply (12V or 24V). The LV124, one of the most important standards for the automotive industry when it comes to general testing requirements, provides strict specifications for auxiliary voltage fluctuations. Various well-known vehicle manufacturers have developed similar factory specifications, such as VW80000, MBNLV124, and BMWGS95024-2-1, which are widely used as product testing standards in the industry. Chroma’s automated test systems come with built-in ISO and major vehicle manufacturers’ regulations, providing a complete and convenient
test solution to help you speed up your product verification process.
Key Features
- Built-in LV124 related test items, compliant with ISO16750-2, VW80000, MBNLV124, and BMWGS95024-2-1
- Fully automated one-button test system that easily reproduces product failure and fault scenarios, saving more than 50% in testing time
- Optional service upgrade ensures that test items are always in line with the latest regulations
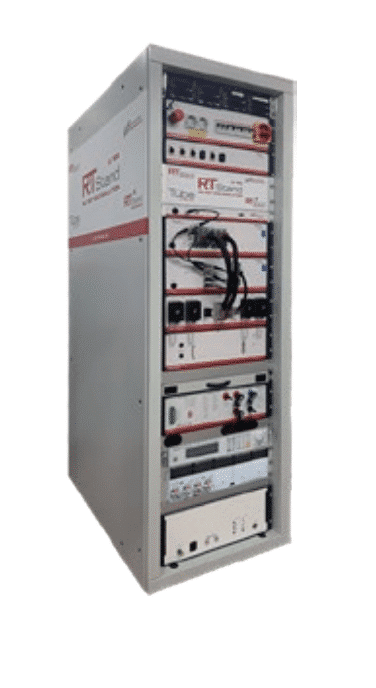
Motor Control Unit ATS 8000
Chroma’s Motor Control Unit ATS can test the inverter’s control panel and drive board, and perform end-of-line (EOL) tests of finished products. The system can test important parameters of the inverter to prevent immobility and unintended movement. This automated test system integrates simulators for DC power supplies, RL loads and inverters for various specifications. In addition to measurement of general electrical parameters, the system can also simulate and verify whether the product
responds correctly to failure, to ensure that it operates normally before assembly to the vehicle.
Key Features
- One-button automated test solution supports reprogramming of test items to meet different requirements
- Supports periodic CAN/CANFD transmission
- Can be customized to meet various testing requirements such as voltage, temperature,
electrical signal, communication, protection, and fault injection
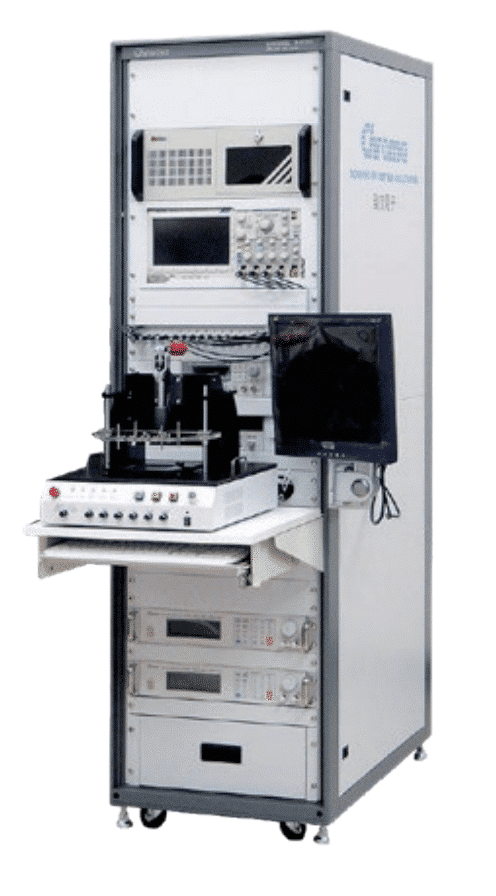
Battery Simulator∣17020/17040/17040E
The 17020/17040/17040E Regenerative Battery Pack Test Systems provide a battery simulator to test battery packs as well as the devices connected to the battery. If the supplier’s battery is not in place when designing and developing the product, the battery simulator can be used to confirm that the system performs as expected. The system can also program the battery’s SOC (state of charge), download different battery curves, and test the product’s charging/discharging status to evaluate the compatibility between product and battery. Test applications include automotive 48V
Mild-Hybrid systems, start-stop 12V systems, motor drivers, and on-board chargers.
Key Features
- Voltage: 30V, 60V, 100V, 200V, 500V, 1000V, 1700V Current: Up to 2600A (17020), 900A (17040), 4800A (17040E) Power: 10kW, 20kW, 30kW, 60kW, up to 1.2MW
- Battery pack output voltage control – Simulate and control the battery pack output voltage by setting up voltage, capacity and SOC – Intelligent efficiency calculation function – Battery pack pre-charge simulation
- Battery pack configuration setup:
Import battery cell data to change battery pack characteristics - Battery cell curve import function:
Import battery cell data to simulate real battery status
Battery Simulator SoftPanel (A170202)
- Supports high-power pre-charge and post-discharge control
- Configurable battery SOC
EV Charging Testing
AC/DC EVSE ATS ∣8000
Because of international differences in charging interfaces and communication protocols, the EV charging interfaces can be broadly divided into four regions (by connector type) and three major standards (CCS, GBT, and CHAdeMO).
This Chroma 8000 AD/DC EVSE test system integrates all the related testing equipment, including AC/DC source, AC/DC load, power meter, DSO, digital meter, and simulators and test items that meet national charging standards. The built-in test items include communication protocols between the charging device and EV. This ensures that the charging device can switch smoothly between different modes as required by the EV’s situation, to maintain its functionality and safety. This system is suitable for R&D, validation and end-
of-line (EOL) testing.
Key Features
- Built-in standard test items compliant with the GB/T18487.1, GB/T 27930, GB/T 34657.1&.2, GB/T 34658, CHAdeMO, SAE J1772, IEC 61851, ISO15118, and DIN70121 standards.
- Electrical characteristics testing, insulation testing, communication protocol testing, and realistic simulation of the actual operation of the EVSE
- Able to simulate the open/short state of each signal line during charging to verify the EVSE’s corresponding protection and response time
- Supports periodic/uninterrupted CP, CAN and PLC transmission
Mobility EVSE ATS ∣8000
The EVSE needs to use electronic detection and signal control technology to properly charge and communicate with the car. At the same time, the electrical energy transferred to the car needs to be measured for billing. In order to maintain optimal operation of the EVSE and to avoid damaging the battery, periodic diagnostic tests are required.
Chroma provides a customized mobile diagnostic test system specifically designed for EVSE verification. It can measure whether the signals and
electrical operations are up to standards and provide reports of test results.
Key Features
- Built-in standard test items compliant with the GB/SAE/IEC/ ISO/CHAdeMO standards, which can be loaded directly without reprogramming
- Supports periodic/uninterrupted CP, CAN and PLC transmission
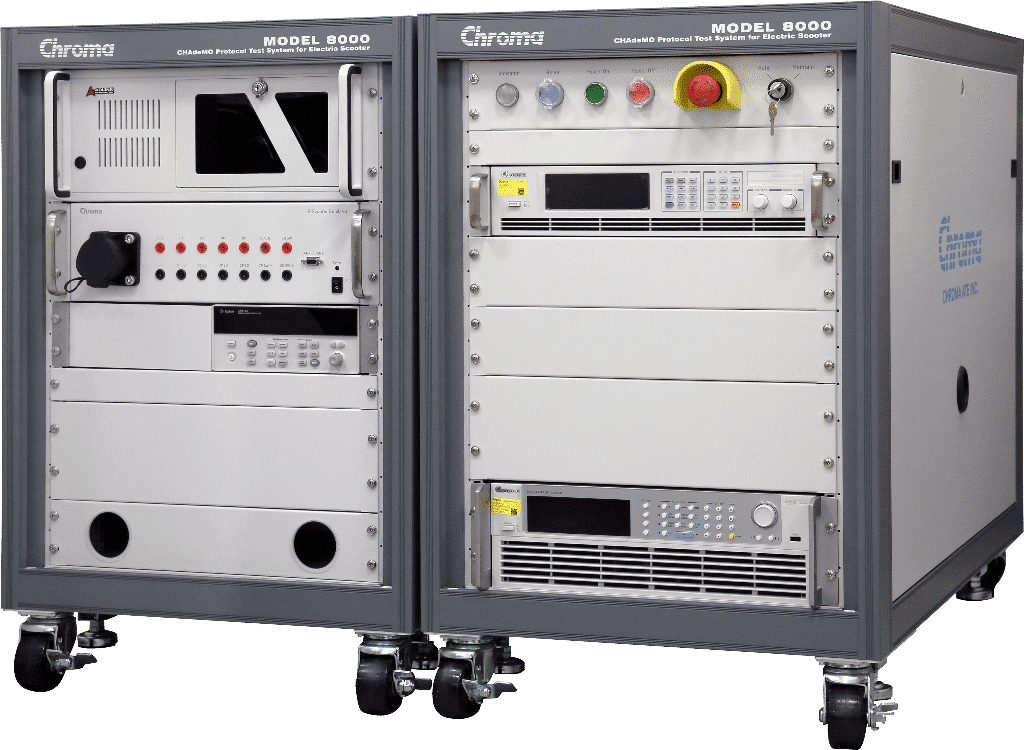
EV Charging Compatibility ATS ∣8000
At present, the supply chains of charging devices and EVs are different in terms of both development and production. Although they follow the same standards, the varying interpretations often cause the vehicle and charging pile to be incompatible for charging and unable to communicate.
To tackle this problem, Chroma delivers the Chroma 8000 EV Charging Compatibility ATS, which integrates all the required equipment: an AC/DC source, power meter, DSO, digital meter, simulators and test items that meet the international charging standards. The built-in test items include:
1. EVSE simulation based on the standards’ requirements, used to test if the EV can perform correctly and react properly when a signal error occurs.
2. Test the EV response using the limit value of signals transmitted by EVSE according to the standards, and ensure the compatibility of various types
of EVSE.
Using real AC-DC EVSE to test charging compatibility carries several risks
- Test waveforms cannot be saved immediately for repeated verification
- When the test results in a fail, it is unclear whether the problem lies with the EVSE or the car
- When the EVSE malfunctions, damage to the vehicle is hard to avoid
- The EVSE becomes obsolete and must be repurchased when national standards are modified
Advantages of using the Chroma test system
- Perform repetitive testing according to various international standards
- All data can be stored with traceability
- Disconnect and protect the vehicle when problems occur during charging
- Update the software whenever the standards are modified
Key Features
- Built-in standard test items compliant with the GB/T18487.1, GB/T 27930, GB/T 34657.1&.2, GB/T 34658, CHAdeMO, SAEJ1772, IEC 61851, DIN70121, ISO15118 test standards
- Provides electrical characteristics tests such as communication protocol tests and simulation of real EVSE operation
- EVSE signal values can be set to normal, limit and over the limit for compatibility testing
- Simulate the open/short state of each signal line during charging to verify the corresponding protection and response time of EVSE
- Supports periodic/uninterrupted CP, CAN and PLC transmission
EV Assembly line (Charge Compatibility) Test Solution

EV Wireless Charger ATS ∣8000
Wireless electric vehicle charging (WEVC) is the latest EV charging technology that can be applied to the cutting-edge EV charging systems equipped with automated driving and wireless power transfer (WPT) technologies. Compared to the conventional cable charger, WEVC is safer and more convenient without any risk of wearing out the charging connector or harm to the operator. Just like the bidirectional on-board charger, modern WPT technology is able to convert the DC power in the energy storage device to AC power paralleled to the public power grid.
Chroma provides an EV wireless Charger ATS for verifying product functionality and safety based on product characteristics and testing requirements. The system is suitable for R&D verification, QA and production lines of EV components and EV manufacturers. The system has been adopted by world-renowned EV components suppliers, iconic EV manufacturers, and national accreditation laboratories.
Key Features
- Chroma WPT test platform providing 3-axis or 6-axis automated tests to reduce time of misalignment and charging efficiency test
- Compliant with SAE J2954 and IEC61000-4-11 for testing voltage dips, short interruptions and voltage variations immunity tests
- Compliant with SAE J2954 and EN60204-1 for testing and simulating AC input voltage distortion waveforms
- Compliant with GB/T 38775 and SAE J2954 for metallic foreign object
detection (FOD) automated test applications
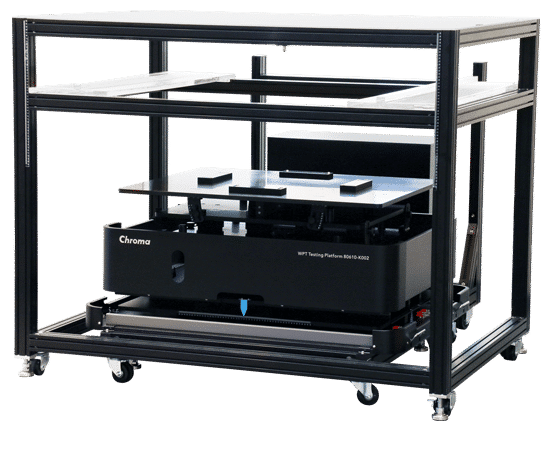
3-axis WPT test platform
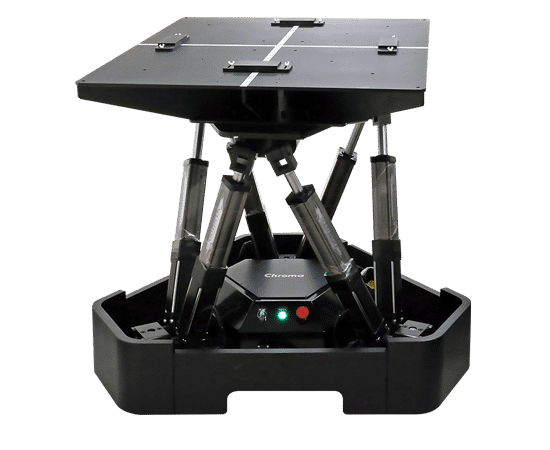
6-axis WPT test platform
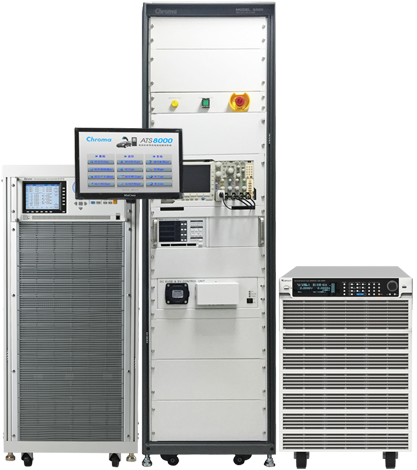
8000 EV Wireless Charging ATS
ATS Software Platform ∣Power Pro
The Chroma 8000 ATS is equipped with Power Pro, an industry-leading software platform that runs on Windows 7+10 and provides users with open software architecture. Test engineers can configure the hardware as desired, program the test items, perform PASS/FAIL tests automatically, and generate reports for analysis.
Key Features
- Expandable hardware support
- Supports GPIB/RS232 instruments and RS485/CAN Bus interface
- Editable test items
- Editable test programs
- User authority and release control
- Editable reports
- Operation log
- Supports Shop Floor Control
- Remote monitoring via internet
Electrical Safety Testing
Most drivers drive their EV every day. To ensure that they can keep doing this safely, electrical safety testing essential. EV operating environments require electrical safety testing to cover the power system, the charging system, the power wiring, the charging cable, the charging connector and the EVSE, all of which play a critical role in safeguarding the performance and safety of the EV.
Standards
- Insulation resistance test (ISO 6469-1, GB/T 18384)
- Withstand voltage test (ISO 6469-3, GB/T 18384)
- Continuity test for potential equalization (ISO 6469-3, GB/T 18384)
- Optocoupler test (IEC 60747-5-5, VDE0884)
- Related standards: UL 2202, UL 2251, ECE R100, UL 2580, GB/T 18488.1
Electrical Safety ATS 8900
Compared with general electrical product testing, electrical safety testing for EVs requires more comprehensive test items and multi-point measurement. The Chroma 8900 Electrical Safety ATS integrates multiple test and multi-point measurement functions to complete all tests in one single
connection.
Wound Component EST Analyzer 19036
- 5 in 1 composite analyzer (ACWV/DCWV/IR/Impulse/DCR)
- Hi-pot test: 5kVac / 6kVdc
- Insulation Resistance (IR) test: 5kV
- Impulse Winding Test (IWT): 6kV
- DCR measurement: 2mΩ~2MΩ – 10-channels 4-wire DCR measurement – Δ/Y motor’s DCR calculation of each phase
- L/Q measurement with model 3252 (option)
Motor Stator Test System 1920
The motor stator is the heart of the electric vehicle. Its quality is directly related to the driver’s safety. In addition to the basic electrical safety testing for EV motor stators
(AC
hi-pot, DC hi-pot, insulation resistance, layer short circuit, and DC resistance), the 1920 can also be used with a vacuum cap to detect pinholes in a vacuum environment (about 1~1.5
Torr) to improve the quality, lifespan, and safety of the motor stator.
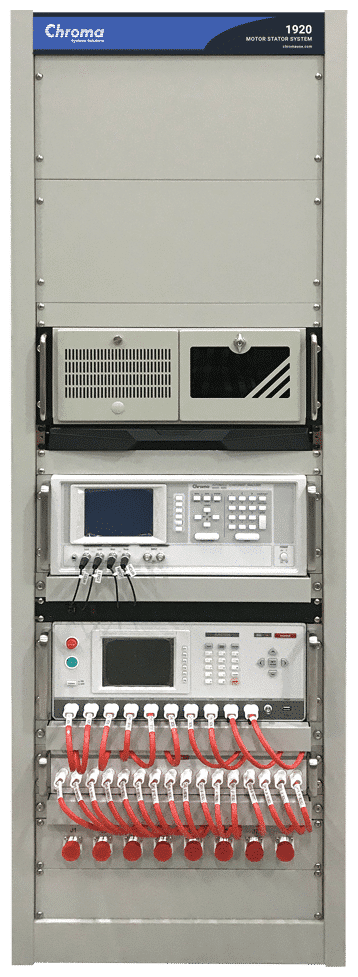
Power Electronics Test Instruments
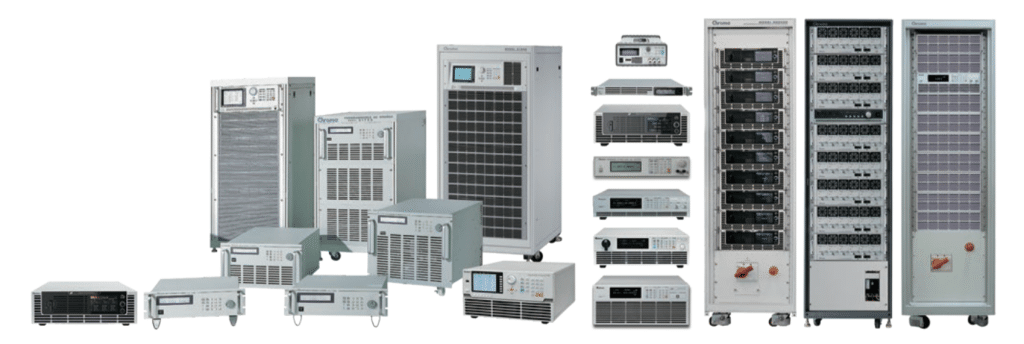
Electric vehicle power converters are generally designed towards two directions: high efficiency, high voltage conversion and high power density on the one hand, combined with battery charging and discharging applications on the other. Chroma offers a wide range of high-power grid simulators, bidirectional DC power supplies, and DC and AC feedback loads. Feeding power back to the grid saves energy and equipment space, and reduces carbon emissions. The equipment is suitable for simulation testing of EV components such as bidirectional vehicle chargers, motor drivers and AC/DC EVSE, and can be integrated into automatic test systems.
Regenerative Grid Simulator 61800 Series
- Output characteristics: – 61809/61812/61815: 9kVA~15kVA/0~350V/DC, 30Hz~100Hz (3U Rack mount type) – 61830/61845/61860/61800-100 : 30kVA~105kVA/ 0~300V (option 400V~900V)/DC, 30Hz~100Hz (cabinet type)
Regenerative AC Load in 1-Phase Mode - Up to 840kVA in parallel (61800-100)
- Four-quadrant AC power supply with efficient energy recycling
- AC grid simulation and optional regenerative AC load enable V2G/V2H/V2L testing
Programmable Bidirectional DC Power Supply 62000D Series
- Output characteristics: 6kW~18kW/0~100V, 600V, 1200V, 1800V/0~540A
62000D - High power density: 18kW in 3U
- Simulation of I-V curves for photovoltaics, batteries and fuel cells
- Easy master/slave parallel & series operation up to 540kW
- Two-quadrant operation: source and load functions
- 3-phase 4-wire universal AC power: 200~480 Vac
- Applications: Charge-discharge testing and longevity testing, bidirectional car chargers, DC-DC converters, energy storage, PCS, motor driver DC-AC power supplies and energy feedback tests
Programmable DC Power Supply 62000E Series
- 3ch output models (1U height): Power rating: 1.7kW/CH ; Voltage rating: 230V/300V/450V/600V
- Single output models (1U height): Power rating: 1.7kW/3.4kW/5kW ; Voltage rating: 230V/300V/450V/600V/800V/1000V/1200V
- Master/slave parallel up to a max of 20kW
- Fixed or Auto-ranging output models
- Standard USB/LAN interfaces, optional APG/CAN FD/GPIB interfaces
- Suitable for EV component testing, active/passive components, D2D modules,
batteries and other multi-channel power supply applications
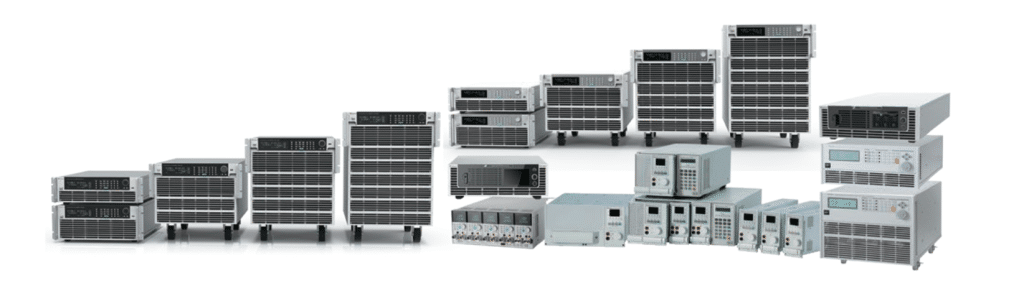
Regenerative DC Electronic Load 63700
- Output characteristics:
6kW~18kW/0~1800V/0~540A - High power density: 18kW in 3U
- CC, CR, CV, CP modes
- Master/Slave parallel control mode with power up to 180kW
- Regenerative up to efficiency 93%
- 3-phase 4-wire universal AC power: 200~480 Vac
- Suitable for long-term durability testing of on-board chargers and fuel cell systems
Programmable DC Electronic Load 63200A
- Output characteristics:
0~24kW/0~150V/0~600V/0~1200V/0~2000A - CC, CR, CV, CP modes
- Master/Slave parallel control mode with
power up to 240kW - User-defined waveforms
- Up to 20kHz high-speed dynamic load simulation
- Suitable for testing automotive components such as D2D, OBC, relay, temperature control MCU, car
generator, fuse, harness, wiper, fuel cell AC impedance and battery inrush current
Regenerative AC Electronic Load 63800R Series
- Output characteristics:
9kVA~15kVA
30Vrms~350Vrms
30~100Hz - Choose between Single-phase and three-phase modes
- Constant Current (CC), Constant Power (CP), Constant
Resistance (CR), Constant Apparent Power (CS) function - Rectified Mode simulates nonlinear impedance loading
characteristics - Lead/Lag Mode simulates inductive and capacitive
impedance loading characteristics - Master/Slave up to 45kVA in 3-phase mode
- Suitable for durability testing of AC EVSE
Regenerative AC Electronic Load 63800R Series
- Output characteristics:
1.8kW~4.5kW
50Vrms~350Vrms
45~440Hz - Measurement: V, I, PF, CF, P, Q, S, F, R, Ip+/-, THDv
- Master/Slave up to 67.5kW in 3-phase mode
- Able to simulate rectified RLC Load mode and suitable for AC voltage distortion VTHD% and dynamic and protection parameters of bidirectional OBCs and AC EVSE inverters with V2H functionality
Battery Cell Insulation Tester 11210
The Chroma 11210 is designed to detect and analyze Partial Discharge (PD) and Flashover in insulators during high-voltage measurements. This feature helps to determine whether lithium-ion battery dry cells have sufficient insulation distance before electrolyte filling, filtering out defective products before they enter the next stage of production or the end market.
Key Features
- Test voltage: up to 1KV (DC)
- Charge current: 50mA max.
- Wide range of Leakage Current (LC) measurement (1pA ~ 20mA)
- Partial discharge/flashover detection for inspection on potential internal short circuits (option)
- Built-in reliable contact check
- Built-in +Flash Test function
- Automatic test with sequence:
charge→dwell→test→discharge
Battery Reliability Test System 17010
The 17010 series test instruments deliver <1mS current response speed and zero crossover distortion during charging and discharging, providing ideal dynamic current output waveforms. The 1mS voltage and current highspeed hardware sampling capability reduces calculation errors in capacity (Ah) and energy (Wh) during long-term dynamic durability testing. The 17010’s output and measurement have good linearity and low uncertainty, which ensures the accuracy and stability of long-term test data. To improve energy utilization, the test equipment with currents above 100A comes with energy recovery functionality, which is highly efficient, generates little heat, and saves space and operation costs. This equipment is especially suitable for power testing and cycle life evaluation of automotive battery cells. In addition, to assess the durability and safety of lithium battery cells under less-than-ideal power conditions, the 17010 also provides an optional test solution for ripple current superposition tests from 100Hz to 20kHz.
Battery Lab Expert
Battery Lab Expert (Battery LEx) is the exclusive software platform of Chroma 17010. Users can quickly reference exist sub-recipes or new sub recipes through multi-layer recipe architecture and edit test plans as required. The independent DUT data management function fully realizes the advantages of sharing different DUT recipes. Flexible recipe parameter editing supports current C-rate setting, OCV-SOC reference, logic variables and other functions, increasing the flexibility of programming.
Key Features
- High precision output and measurement up to ±0.015% of full scale
- Fast current response up to 100µS
- High sampling rate up to 10mS
- High single point transient sampling rate up to 1mS
- Channel parallel output up to 1200A
- Energy recycling during discharge
(AC/DC bi-directional regenerative series) - Waveform simulation
(current/power modes) - Ripple current superposition test
function (optional) - Multi-level safety protections
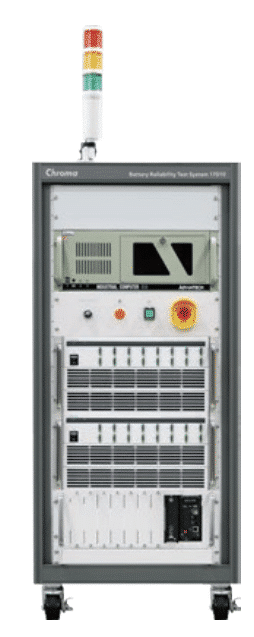
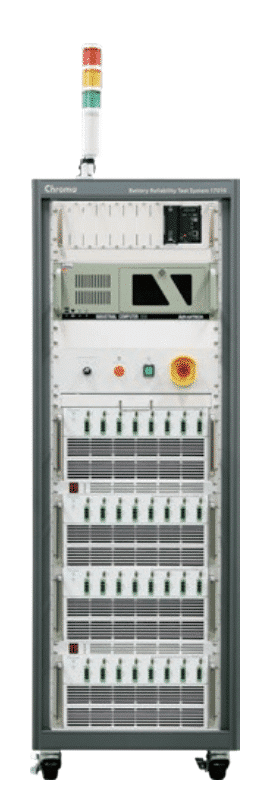
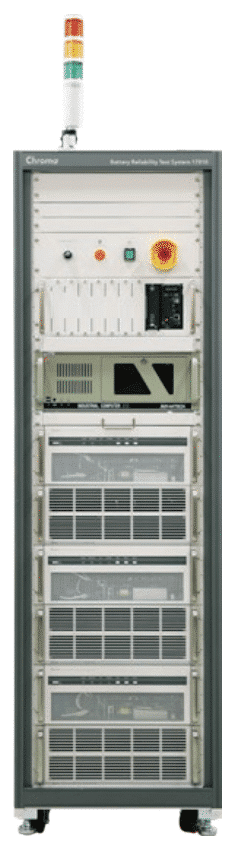
High Power Regenerative Battery Pack Test System 17040 & 17040E
The Chroma 17040 Regenerative Battery Pack Test System is a high precision system specifically designed for secondary battery module and pack tests. It has an energy regenerative function to greatly reduce power consumption during discharge. Besides its economic benefits, it also solves the intractable problem of heat generated in the operating space and meets the requirements of environmental protection. The system has built-in parallel channels and a dynamic driving profile simulation function that increases operating efficiency and flexibility. The driving profile simulation is in line with the ISO, IEC, UL and GB international testing standards.
- Supports CC/CV/CP/DCIR charging/discharging mode
- Dynamic power or current waveforms simulate the drive cycle or any real-world application
- Current response speed (0 to 90%): 1ms
- Current slew rate: 2ms (-90% to 90%)
- Fastest report sampling speed: 1ms (Waveform mode)
- System integration capability: temperature chamber, multi-channel voltage/temperature data logger, and BMS
- Auto bidirectional voltage source with optional battery simulator function
- Regenerative battery energy discharge >90%
- Supports loading simulations of real vehicle
current waveforms - Dynamic battery discharge and charge function
- Supports up to 10ms periodic CAN Bus
communication via BMS - Supports DBC file import for CAN signal reading
and calling - Supports UDS diagnostic service command set
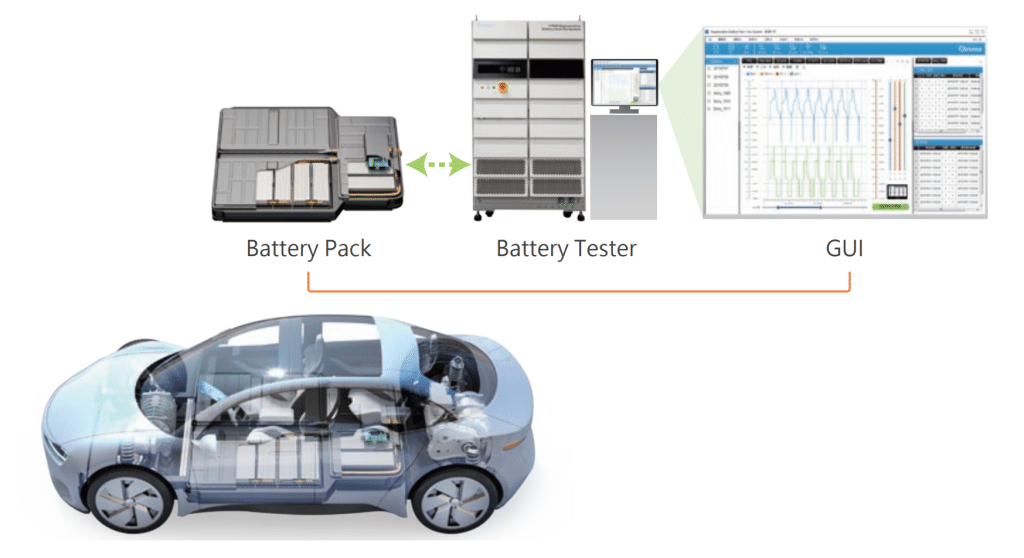
EV Battery Testing
Regenerative Battery Pack Test System ∣17020 & 17020E
The 17020 Series can be tailored to each customer’s requirements in terms of DUT numbers and specifications. It supports up to 60 channels of independent or parallel operation. The 17020E is specifically designed for testing battery modules and 100V Battery packs during mass production. Both systems are equipped with multiple independent channels to support dedicated charge/discharge tests on multiple battery modules and packs, each with discrete test characteristics. Channels can easily be paralleled to support higher current requirements and use the equipment to its full capacity.
- High precision current/voltage measurement
Voltage:0.02% rdg.+0.02% rng.
Current:0.5% rdg. + 0.05% rng.. - Dynamic charge/discharge current waveforms to simulate the drive cycle or actual application
– Ability to import current waveforms from an Excel file and save a maximum of 720,000 points to memory
– Maximum charge and discharge current switching speed of 10ms - Built-in DCIR function (IEC61960-2004)
- Battery discharge energy recovery function. Regenerative battery energy discharge up
to 85% efficiency (regenerate to grid) when the rated power is over 20%
Charger and Discharge Test Software Platform ∣Battery Pro
Battery Pro is a specifically developed software platform for testing secondary battery packs with multilingual interface support (English/Traditional Chinese/Simplified Chinese) that can be used by the 17040, 17020 and 17020E systems. It features real-time status monitoring, an icon manager, user authority management, fault record tracking, security detection, and data storage and recovery during power failure.
The system can integrate temperature chamber, data logger, and communication interface devices through Battery Pro, and read external parameters to enable protection or cut-off conditions during the charging or
discharging process.
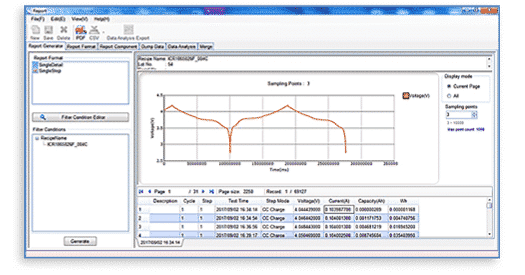
Battery Management System ATS 8700
The Battery Management System (BMS) manages the batteries. It is usually capable of
measuring battery cell voltage, and can prevent abnormalities such as overdischarge,
overcharge, and overtemperature from occurring. Many functions are gradually added in
the wake of technology development. Common functions include voltage measurement,
communication, SoC and SoH estimation, abnormality warning and protection, equalization
(passive or active), other control circuits (such as battery loop relay control), temperature and
current measurement, and diagnostics.
The Chroma 8700 BMS ATS is a test system for verifying battery pack BMSs. It is equipped
with a multi-channel battery cell simulator, high-precision real current and high voltage
source, programmable temperature simulator and isolation resistance simulator. The system
can be configured to support master/slave and centralized architecture based on the DUTs
specific needs.
Key Features
- Battery cell simulator
– Cell state simulation test and calibration: 5V/ 5A/ 16CH - High precision real current source
– Current testing and calibration: charge/discharge current 600A or larger - High precision voltage source
– High voltage testing and calibration: 450V/600V/1000V - Temperature simulator
– Temperature testing and calibration - Isolation resistance simulator
– Insulation measurement circuit test and calibration: Insulation resistance simulation
under high voltage 1000V - On-board Charger signal simulation: CC, CC2, CP signal
- Customized test items
- CANBUS communication related tests
– Periodical CANbus frame with check sum (check sum customization service):
min. 10ms per CAN frame
– Equipped with Unified Diagnostic Services (UDS) battery management capability
– Supports *.dbc format parsing
16CH Battery Cell Simulator 87001
Chroma 87001 Battery Cell Simulator is a high-precision, programmable, and bidirectional DC
power source with both voltage source and current source functions. In addition, the model
can be used as a multi-channel DC power supply or an electronic load. A single simulator has
16 channels; the voltage and current of each be set separately via the software interface.
Key Features
- Battery cell simulation mode: Maximum 480 cells in series for simulation
Channel power 25W
Channel voltage 5V
Channel current 5A (parallelable) - 4 current ranges (0~250uA/0~500mA/0~5A/0~9A super modes)
0~250uA : Used to determine whether the levels of leakage current are too high
0~500mA : Used for passive balancing test requirements
0~5A/9A : Used for active balancing test requirements - Control the battery simulator remotely with the Softpanel
– Individually adjust the voltage of each battery string
– Access the battery cell curve loading function to view voltage changes based on the
voltage compared with SOC
– Set the voltage change procedure: OVP/UVP/OVP release/UVP release test - Can be integrated via software commands to become an HIL test system for BMS
Battery Pack EOL ATS 8720
The Chroma 8720 ATS can be applied to testing battery packs in the end of line (EOL)
phase. The system’s comprehensive Pass/Fail tests cover the mechanism assembly
process, pressure insulation, BMS communication, internal high voltage relay parts,
battery balance, and temperature measurement, all before the product reaches the end
of the production line.
The application of this test solution is not limited to production lines. It can also be used
to carry out a comprehensive inspection of the incoming battery packs near the end of
the R&D phase or on EVs and energy storage stations. Automated tests minimize human
error and ensure personal safety, which is crucial for EVs, electric scooters, and battery
modules for energy storage systems.
Key Features
- One-stop integrated safety testing reduces number of times battery packs are loaded
and unloaded - Charge and discharge power range: 5kW~500kW
- Charge and discharge voltage/current range: 0V~1,200V/0A~2,600A
- Standard test items: insulation test, electrical test, BMS communication test, performance test
- Automatic switch to testing when used in tandem with automated production line
- Automatic uploading of traceability reports when integrated with Manufacturing Information System (MES)
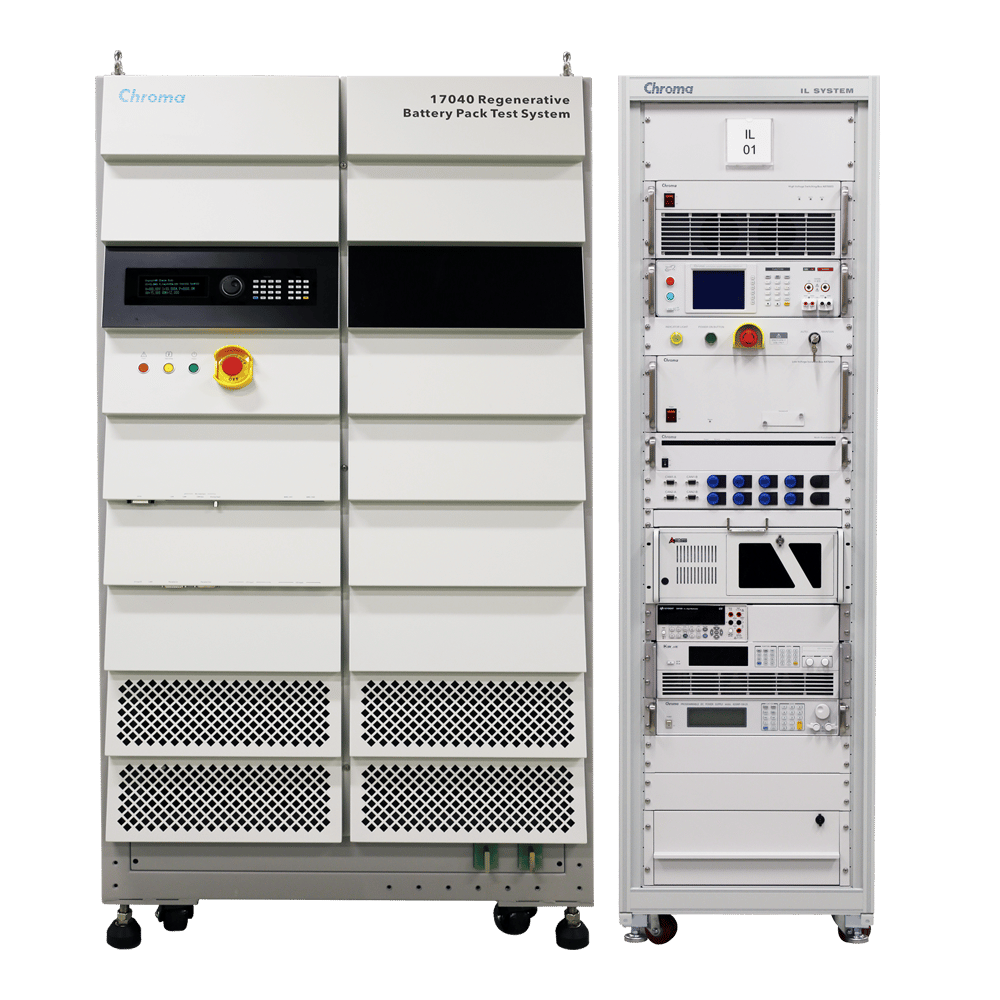
Battery Module / Battery Pack Production Line Test Process
Chroma provides customized ATSs for each station in the battery pack production lines in close cooperation with automation companies, to perform high-efficiency production verification including cell sorting tests, module assembly inspection, BMS PCBA tests, and battery pack EOL tests.
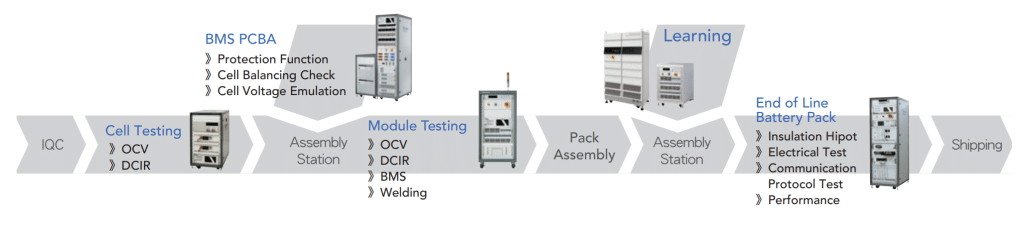
Battery Balance Maintenance ATS 8700
When the battery packs are used or placed for an extended period of time, functional test and maintenance are required to extend the battery
cell life. The Chroma 8700 Balance ATS can inspect the battery module, cell internal resistance and voltage status in the battery pack to ensure the
internal unit is in good condition. In addition, it has module/battery cell independent charging and discharging for balance as well as temperature
status monitoring functions.
Battery Pack Power HIL Testbed 8610
Chroma 8610 is designed for the development phase of battery modules and packs. With real-time hardware and software with open architecture at its core, it provides users with a
flexible and powerful dynamic testbed. Besides basic test functions such as vehicle driving cycles importing, CAN signal monitoring, fault injection, insulation measurement, and EVSE charging simulation, Chroma 8610 can execute the most important compound scenarios for real vehicle and composite operation conditions with the highest risk of failure (e.g. physical and communication signal errors during cyclic discharge). The system greatly improves R&D efficiency by performing in-depth tests on battery packs without the need to test a real car.
Key Features
- Integrated FIU hardware that simulates fault injection and improves ISO 26262
functional safety testing. - Supports importing various Simulink real-time models, to verify on-road battery dynamic charging and discharging through standard driving conditions like NEDC and WLTP.
- Supports CAN, CAN FD, LIN communication interfaces.
- Integrated AC/DC EVSE charge interfaces, incl. CAN Bus and PLC signals. for various compatibility tests
- Real-time monitoring of timing sequences, incl. high power relay open/close, initial power output, and CAN signal.
- Integrated Hi-Pot safety analyzer, to measure, compare battery insulation and grounding status.
- Extensive modular hardware that ensures test accuracy and repeatability; expandable
according to users’ needs. - Supports upper-level automated test software through ASAM XIL and ASAM XIL-MA.
- Independent PLC real-time monitoring ensures operator safety during testing.
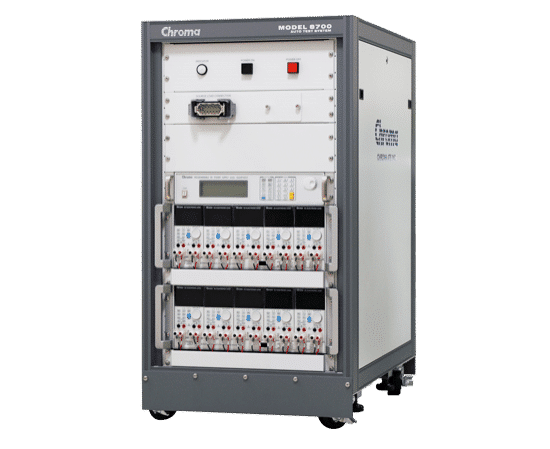
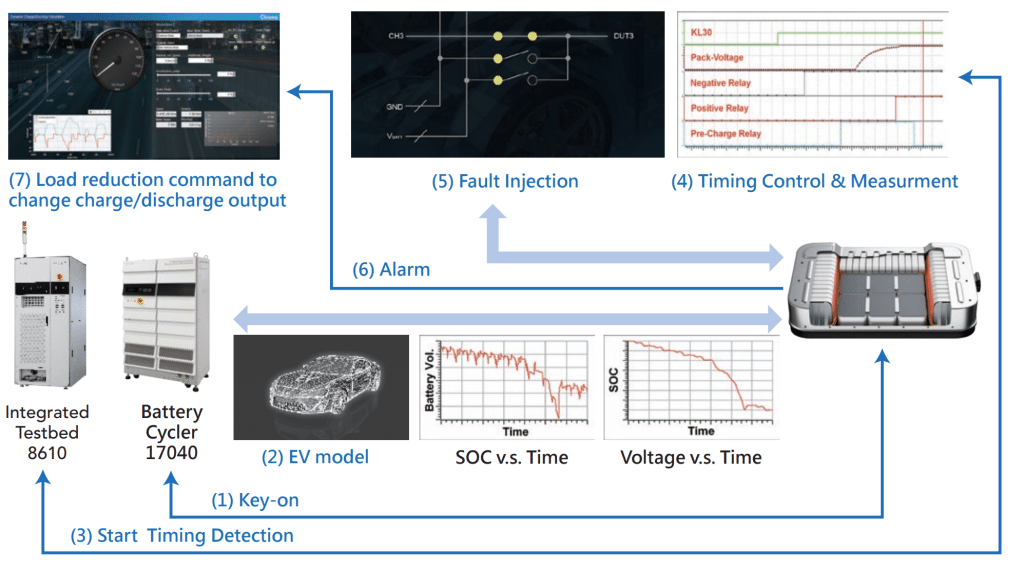
Electric Propulsion Testing
OBC and DC-DC Converter Power HIL Testbed 8620
Chroma 8620 OBC and DC-DC Converter Power HIL Testbed is suited to testing electric vehicle charging systems and powertrain components. The hardware configuration can be adapted according to DUT specifications, with options including a programmable DC power supply, programmable DC electronic load, digital power meter, and oscilloscope. Chroma 8620’s platform can be expanded and shared, as well as applied to different system architectures.
Chroma 8620 is specially designed for research and development of on-board chargers (OBC) or DC-DC converters. Its flexible software provides user interfaces for operation and monitoring of manual and automated test functions and automatically generates comprehensive test reports. Users can quickly conduct large numbers of repeated tests, improving test coverage and efficiency
Key Features
- Supports customized hardware configuration, platform sharing, and expansion
- Flexible software platform
– Easy to operate and monitor user interfaces
– Manual testing capabilities
– Automated test program editing
– Automated test report generation
– Supports LabVIEW, C/C++, Python, .NET languages
– Supports data recording - Supports CAN, CAN FD, LIN communication
- Real-time monitoring for safety testing with an independent PLC system
- Supports signal fault injection simulation (open circuit, short circuit)
- Import a variety of Simulink Model-Based real-time vehicle models
- Supports UDS diagnostics (ISO 14229)
- Supports GBT, QCT standards testing
On-Board Charger (OBC)
Standards Testing
- Normal Functioning Test
- Abnormal Functioning Test
- Communication Abnormality Test
- Signal Fault Injection Test
- Model Abnormality Test
DUT Functional Testing
- Normal Functioning Test
- Abnormal Functioning Test
- Communication Abnormality Test
- Signal Fault Injection Test
- Model Abnormality Test
DC-DC Converter
Standards Testing
- Normal Functioning Test
- Abnormal Functioning Test
- Communication Abnormality Test
- Signal Fault Injection Test
- Model Abnormality Test
DUT Functional Testing
- Normal Functioning
- Abnormal Functioning
- Communication Abnormality
- Signal Fault Injection
- Model Abnormality
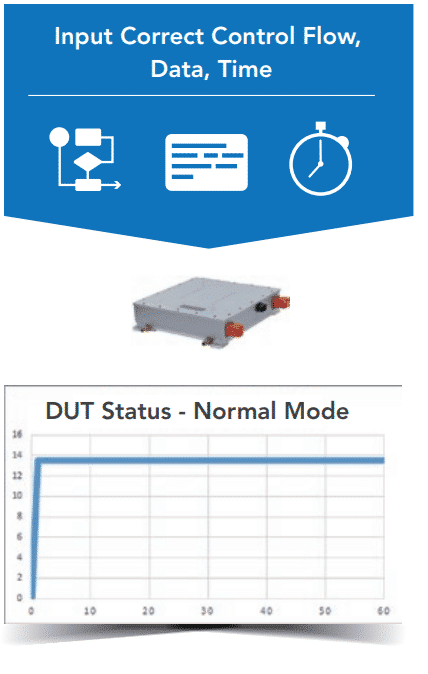
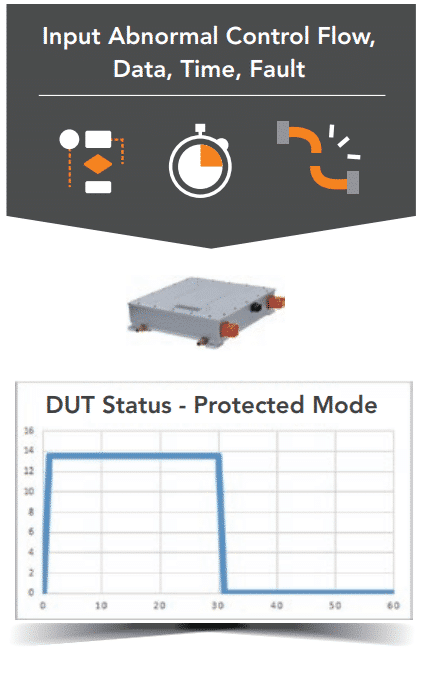
BMS HIL Testbed 8630
The Chroma 8630 BMS HIL Testbed is a test platform that includes related modules such as real-time systems, high and low voltage instruments, human-machine interfaces, test project editing, system wiring and fixture integration. It can simulate various BMS input and output signals to perform a closed-loop test for real-time response requirements, as well as verification of various single functions of the BMS (e.g. monitoring and power calculation). The testbed’s open software and hardware architecture provides high convenience and flexibility for system function adjustment and future modification.
In addition, the 8630 is equipped with vehicle battery, drive system, road simulation and driving behavior models. After being fed actual vehicle conditions, it can carry out test items such as charge and discharge, CAN signal measurement and control, fault injection, insulation measurement and EVSE charging simulation. The system can also verify the fault conditions for the most important compound operation scenarios (such as a failure of the safety mechanisms during actual operation of the vehicle). This kind of system-level, compound working condition test capability greatly improves the test scope and reliability and eliminates the need to test a real vehicle.
Key Features
- Integrated Fault Injection Unit hardware injects simulated faults for comprehensive ISO 26262
functional safety testing - Import a variety of Simulink Model-Based real-time vehicle models to verify the dynamic charging and discharging performance of EV batteries, under conditions that comply with NEWC, WLTP and other international standards.
- Integration of the battery cell and current simulator enables real-time changes in dynamic cell voltage, balance current, and large actual current in the battery system
- The battery cell simulator is equipped with 5V/5A power to deliver the range of energy required for the cell’s passive and active balancing functions
- Integrated Hi-Pot withstand voltage test equipment can measure and compare BMS insulation and grounding status
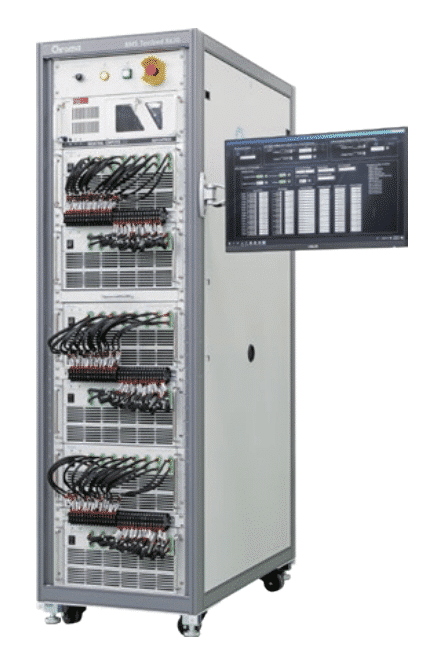
E-Propulsion Test System 1210
Chroma 1210 E-propulsion Test System is suitable for performance calibration and verification of vehicle power systems. The versatile software can load high-fidelity dynamic vehicle models for simulation & verification of electrical and mechanical components. The manual and automatic operating interfaces offer flexibility and convenience to synchronously record essential system parameters such as voltage, current, power, rotational speed, torque, and temperature, which are used to calculate the efficiency of the motor and controller and generate the torque curve graph. With four-quadrant operation capability, the E-propulsion Test System can maintain constant torque load below the rated speed (zero speed or even reverse rotation) and constant power above the rated speed. The test bench frame has been developed especially for the requirements of dynamic applications. The modularized mounting bracket makes it easy to fit the fixtures onto motors of various sizes.
Key Features
- Power HIL testing for EV motors, motor controllers, gearboxes,
and e-drive systems - Power up to 500 kW , rotational speed up to 18,000 rpm
- Various motor mounting options
- Import a variety of Simulink Model-Based real-time vehicle models
- Supports identification of motor vibration characteristics
- Supports test part bus systems CAN, CAN FD, EtherCAT
- Cooling methods IC06 (self-ventilation)/IC86W (heat exchanger)
- IP23 (self-ventilation)/IP54 (heat exchanger) protected
- Additional high/low temperature environmental chamber (option)
- Follows standards:
– GB/T 18488.1-2015
– GB/T 18488.2-2015
– Industry-developed test standards
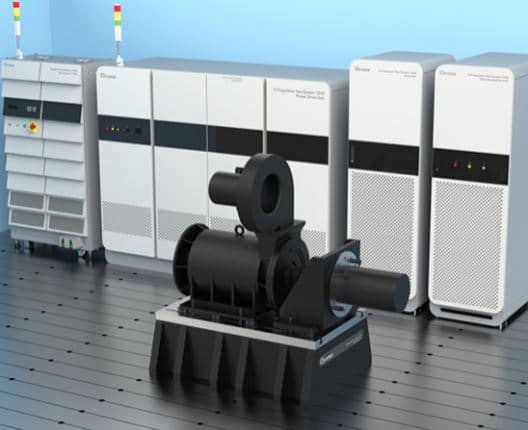
MORE FROM THE MEDIA HUB
February 2, 2024
Future Propulsion Conference 2024
READ MOREJanuary 15, 2024
A dedicated resistance meter? Here is when it makes sense…
READ MOREDecember 4, 2023