Table of Contents
What is Hipot testing?
The main purpose of Hipot (High Potential Test) is for testing the insulating capability of a DUT (Device under Test).
Testing is also able to check for faults in the manufacturing process such as:
- Scrapes
- Pinholes
- Spacing
- Crimps
- Heat Material Build-up
- Moisture
- Contaminants
Leakage current is measured to determine whether the insulation of a product is able to withstand high voltages without breaking down. The result can also be used to determine the quality of the insulation.
Hipot Test
One safety test that is frequently used is the pot test. The terms high potential, dielectric withstand, and Hipot all refer to withstanding tests. Hipot tests are primarily used to evaluate the DUT’s insulating capabilities (Device under Test). Apply a high voltage to the test point while the equipment is running to check for insulation breakdown or electrical flashover/ARC. Four categories of insulation exist Basic, Supplementary, Double, and Reinforced. Since the product inside may be over dirt, moisture, or other factors that cause discharge along the surface, a Hipot test can be used to determine whether the product’s internal circuit design has issues with distance along the surface or insufficient insulation.
Leakage Current Test
The current is brimmed over as it flows through insulation impedance, which we call leakage current. When the current contacts the human body and flows through the human body to Earth, electrical damage occurs. Leakage current testing, withstanding voltage testing, and grounding protection testing are distinct from one another because they involve running equipment. When testing, the leakage current adds an impedance circuit that simulates the human body; this allows it to simulate the amount of leakage current that would actually flow through the body.
Insulation Resistance Test
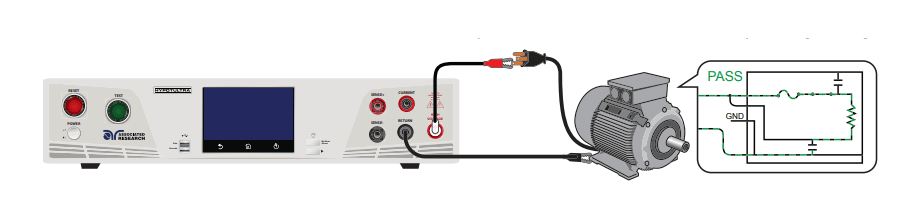
Insulation resistance testing and DC withstand testing are very similar in that they both apply DC voltage (50~1000V) to two points of contact to determine whether a product is defective or not. The insulation resistance value cannot be less than 10MΩ when the test voltage is 500V or 1000V. Insulation resistance testing is a non-destructive test that can determine whether or not insulation is adequate. In some regulations, the insulation resistance test is performed first, followed by the withstand test. When the insulation resistance test fails, the withstand voltage test is unable to pass as well.
Ground Protection Test

Ground protection is tested using two methods: ground continuity (GC) and ground bond (GB). The aim of the ground protection test is to protect users from electrical hazards such as touching equipment when an unsuitable current is generated and flows to the earth. As a result, it is necessary to determine whether there is a high resistance value or a lack of load capacitance between the DUT accessible part and the E terminal of power.
One ampere of DC current is fed into the power terminal to test ground continuity and confirm that the resistance between the two ends is less than one ohm. Ground bond testing is performed from the power terminal to the input terminal at 25A or 1.5 times the rated current, whichever is greater (50/60Hz). Resistance standards are typically less than 100mΩ. Different safety standards have different test multiples, some of which are two multiples of current and have different conditions for setting. For example, if the DUT has a 5A/220V rated fuse, the test current value should be determined by the rated current of the fuse.
ARC Test
ARC is a type of electrical discharge that occurs when the insulation capability is insufficient. If ARC occurs multiple times, the system will fail. ARC occurred may be within 10us, thus resolution and sensitivity of ARC judgement will influence the test result.
What is the difference between a Megger and Hipot?
‘Meggers’ test low to medium voltage with a typical voltage between 600V – 2000V
Whereas Hipot testing applies significantly higher voltages typically above 15,000V
How long is a Hipot Test?
Depending on the standard Hipot testing can be anywhere from 10 milliseconds to 5 minutes.
For most standards including those covered under IEC 60950 the required time is 1 minute. However, a typical rule of thumb is 110 to 120% of 2U + 1000 V for 1–2 seconds.
Is a Hipot test destructive to the tested part?
Possibly. Hipot testing can cause insulation stress and damage if the voltage and/or duration are too high for the specific design. Because insulation damage can be difficult to detect, production Hipot testing is a trade-off between test voltage and component damage.
One method of determining a safe production test voltage is to dielectric breakdown test a sufficiently random sample to failure. Based on a leakage limit or arcing, the test voltage is increased until the dielectric fails. The Hipot test would then be carried out at a lower voltage with an adequate safety factor.
To avoid causing insulation damage, avoid applying Hipot voltage in excess of the product rating. It is also important to avoid repeat testing. Lower voltage should be considered for repeat testing to avoid insulation damage.
How do I choose a hipot tester?
When looking for a Hipot tester is best to look for a tester that is able to supply two times the working voltage + 1000V.
It is also important to check output voltage as it can either be AC or DC.
Also testing methods can be automatic, semi-automatic, and manual depending upon the model.
Should I test in AC or DC?
When performing a Hipot test it is important to know if the standard you are adhering to allows you to perform a test in DC. Check your agency specification.
Some standards will allow tests to be performed in d.c. however, they often require the test to be performed at the peak value of the a.c. test.
IEC 60601-1 ‘Alternatively, a d.c. test voltage equal to the peak value of the a.c. test voltage may be used.‘
The applied test voltage must be the same value whether it is AC or DC because a Hipot test stresses the insulation of a DUT with high voltage.
RMS x 1.414 = Peak = DC Equivalent
The DC voltage must match the peak of the AC waveform during a DC test by using the formula shown below:
DC Hipot Test Voltage = (Nominal Input Voltage) * 2 + 1000V
Uncertain of the Hipot test voltage? Always consult the relevant agency standard as they may call for a different multiplier for the conversion of the AC to DC Hipot test voltage.
AC Advantages
- No voltage ramping requirements due to the polarity of ACV.
- Insulation testing in both polarities.
- Commonly accepted by safety agencies and standards.
- Discharging the DUT is not necessary
AC Disadvantages
- Measures only the total leakage current
- Requires a large Hipot transformer due to measuring the total leakage current.
- Higher cost
DC Advantages
- Leakage Current is purely resistive, actual value.
- No reactive current, avoid false failures.
- Cost-effective, less current required.
- Easier to perform on capacitive DUT’s.
- Lower current, lower risk to the operator.
DC Disadvantages
- Requires a ramp up
- Have to discharge DUT at end of testing
- Not always widely accepted by safety agencies and standards
- Only stresses insulation in one polarity.
The production-line Hipot test is used to determine whether the construction of a production unit is similar to the construction of the unit that was subjected to type testing. This test is typically shorter in duration to ensure the unit is not damaged during testing.
DC Hipot tests usually need to add ramp time and fall time, because most DUTs are with capacitance and cause charging current generated. For charging current steady, ramp time is needed for buffering then leakage current won’t over high because of charge current and judge as FAIL. The more DUT capacitance, the more ramp time.
DC Hipot tests cause DUT discharge and thus require a period of time for discharging after the Hipot test has ended. Some Hipot test equipment will decrease fall time to the minimum and mark danger warnings before reaching discharge standards for protecting the testers from electrical shock.
Class 1 vs Class 2
Electronic devices that are tested are put into two categories, class 1 and class 2. Class 1 devices include a safety ground circuit and have a line neutral and ground whereas class 2 only has a live and neutral.
Typically there are two voltages used to conduct isolation testing; 3kVAC and 4kVAC. For IT and industrial equipment, the international safety standard IEC60950-1 applies to AC-DC power supplies.
This stipulates that your product must pass an input-to-output isolation test of 3kVAC. The IEC61010 standard applies to test and measurement equipment and also requires the 3kVAC test.
Medical equipment is covered by standard IEC60601-1. Input-to-output isolation tests need to be conducted at the higher voltage of 4kVAC in order for the design to comply with this standard.
European Standards
Standard | Description |
EN 50091 | Uninterruptible Power Supply (UPS) |
EN 50144 | Safety standard of portable electronic motor appliance |
EN 60034 | Rotatory electronic mechanical equipment |
EN60035 | Household appliance equipment |
EN 60204 | Safety standard of mechanical equipment |
EN 60335 | Safety standard of household appliance |
EN 60950 | Safety standard of information product and enterprise information equipment |
EN 60967 | Safety standard of electric blanket, electric pad and household related heating equipment |
EN 60968 | Safety standard of electric lamps for general lighting |
EN 61010 | Safety standard of measuring, monitoring and laboratory equipment |
EN 60601 | Safety standard of medical equipment |
What is the difference between Dielectric voltage withstand testing, high potential testing, and Hipot testing?
Nothing, they are interchangeable depending on the indutry.
MORE FROM THE MEDIA HUB
February 2, 2024
Future Propulsion Conference 2024
READ MOREJanuary 15, 2024
A dedicated resistance meter? Here is when it makes sense…
READ MOREDecember 4, 2023